Introduction to Veloxint Nanocrystalline Chromium (VCr)
This system exhibits extraordinary corrosion resistance, even at high temperatures.
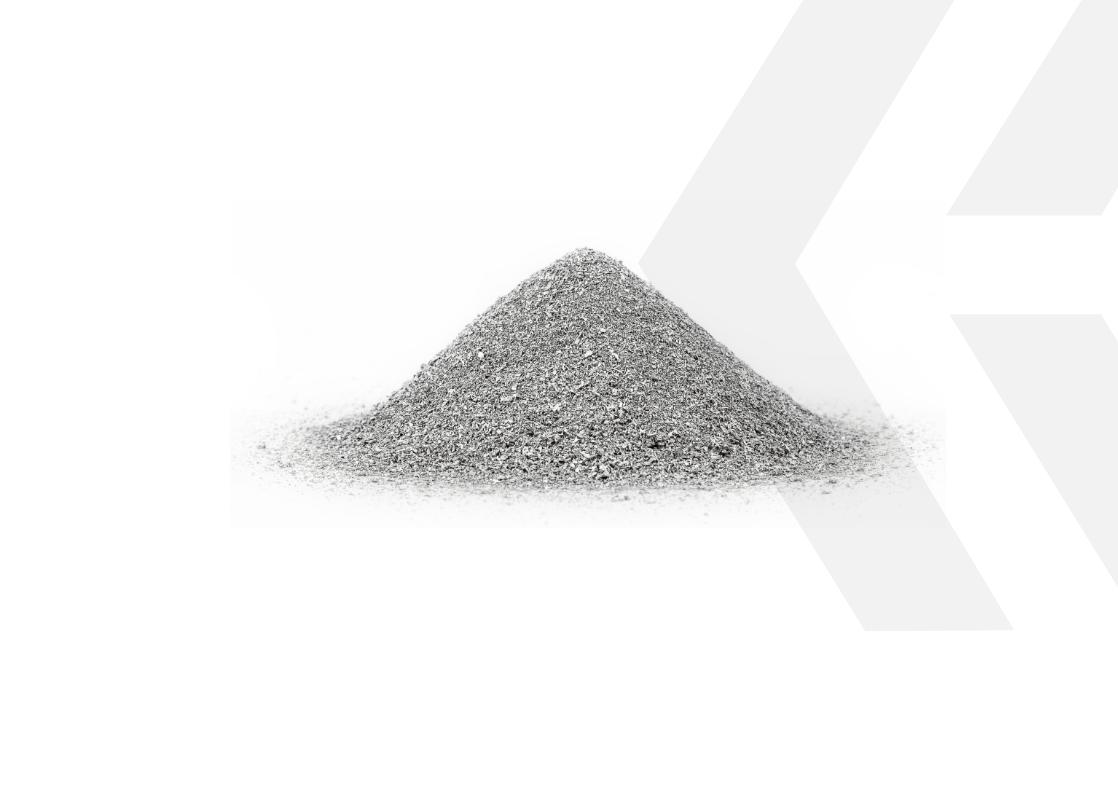
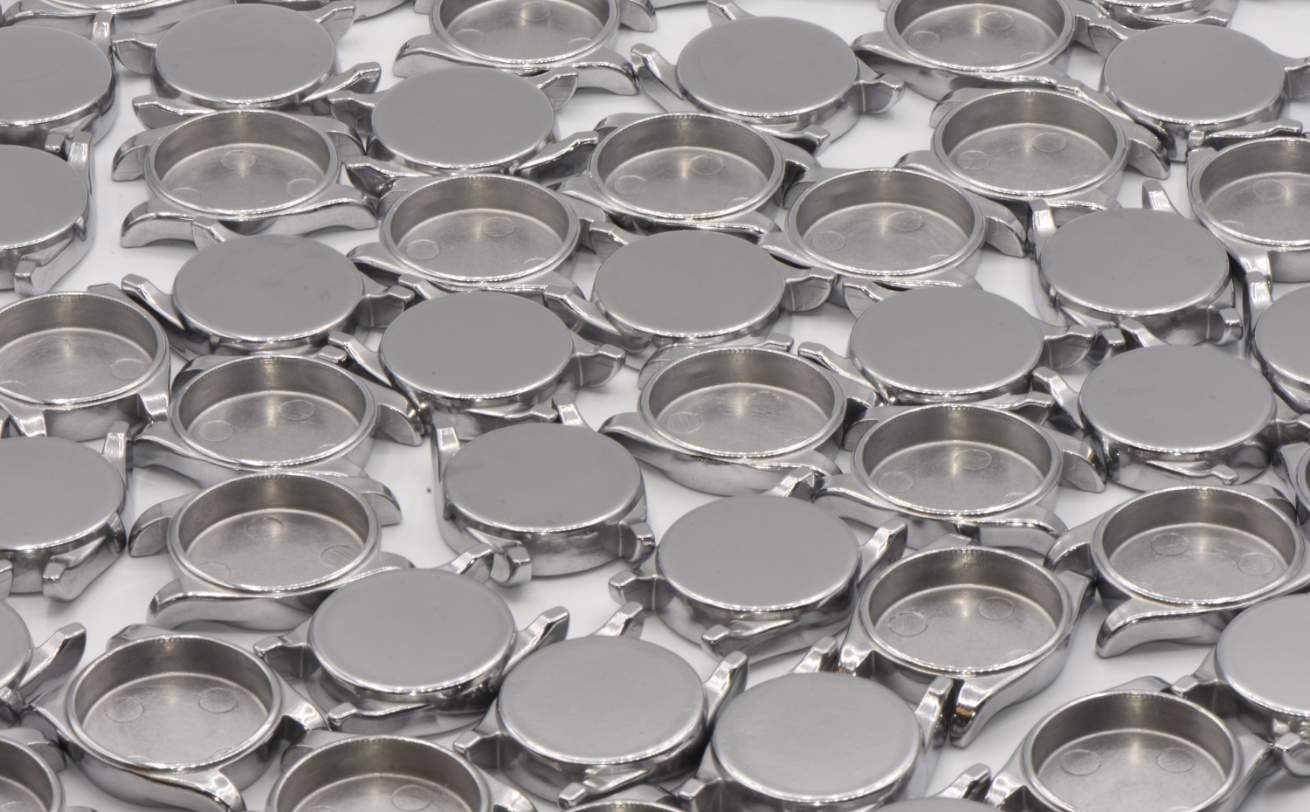
Applications
- Industrial Corrosion Resistant Applications
- Jewelry
- Medical Implants
- Chemical Processing
- Nickel Super Alloy Replacement
Powder Properties
- Media particle size 11 μm
- Tap density 4.0 g/cc
- Pycnometer Density 7.4 g/cc g/cc
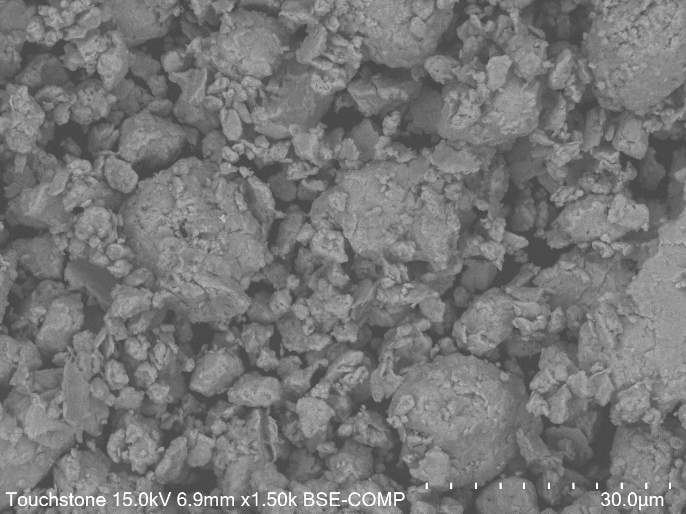
Advantages
- Nanophase Separation Sintering
- Makes it densify extremely well
- Excellent Corrosion Resistance
- Non-Magnetic - includes no iron
Mechanical Properties | Value Range*[unit] | |
---|---|---|
Tensile Yield Strength | 930 MPa | 135 ksi |
Compressive Yield Strength | 1,875 MPa | 272 ksi |
Young’s Modulus | 242 GPa | 35.1 Mpsi |
Poisson’s Ratio | 0.24 | |
Vickers Hardness | 400 HV |
Thermal & Electrical Properties | Value Range*[unit] | |
---|---|---|
Coef. of Thermal Expansion | 8.8 µm/m-°C | 4.9 µin/in-°F |
Specific Heat | 0.46 J/g-K | 0.11 btu/lb-°F |
Thermal Conductivity | 19.4 W/m-K | 11.2 btu/ft-hr-°F |
Electrical Conductivity | 1.90E+06 S/m | 5.79E+05 S/ft |
Learn More About Our Processing Techniques
Typical Part Properties
Physical Properties | Value Range* [unit] | |
---|---|---|
Density | 7.05 g/cm3 | 440 lb/ft3 |
Mechanical Properties | ||
Compressive Yield Strength (25°C)⁺ | 1,875 MPa | 272 ksi |
Compressive Ultimate Strength (25°C)⁺ | 2,300 MPa | 333 ksi |
Plastic Strain in Compression (%) | >10% | |
Young’s Modulus | 242 GPa | 35, l 00 ksi |
Poisson’s Ratio | 0.24 | |
Shear Modulus | 98 GPa | 14,200 ksi |
Vickers Hardness (HV1 )⁺ | 350 | |
Thermal & Electrical Properties | ||
Coef. of Thermal Expansion (30-300°C) | 8.8 µm/m-°C | 4.9 µin/in-°F |
Specific Heat - 25°C | 0.46 J/g-K | 0.11 btu/lb-°F |
Specific Heat - 1200°C | 0.8 J/g-K | 0.19 btu/lb-°F |
Thermal Conductivity - 25°C | 19.4 W/m-K | 11.2 btu/ft-hr-°F |
Thermal Conductivity - 1200°C | 27.8 W/m-K | 16.1 btu/ft-hr-°F |
Electrical Conductivity - 25°C | 1.90E+06 S/m | 5.79E+05 S/ft |
Chemical Corrosion & Wear Properties | ||
ASTM G28A Boiling Sulfuric Acid | 0 mm/yr | 0 in/yr |
ASTM B117 Salt Spray | No Corrosion, 96 hrs | |
EN 1811 Nickel Release | Compliant | |
ASTM G65A Volume Loss | 48.85 mm3 | 0.003 in3 |
- Manufacturing Method Dependent⁺